概要
この記事では高圧ガス甲種機械の1科目である保安管理技術について解説します。
学識とは違い選択肢から正しい組み合わせを選ぶ問題なので、カンでも当たる可能性はあります。
ただし出題範囲が広いため、勉強をしていないと馴染みのない分野は全くわからないという状態になります。
最低でも2択くらいまで選択肢を削れるよう勉強しておきたいところです。
保安管理技術の出題分野
保安管理技術は全部で15問あり、9問(60%)程度正解すれば合格となります。
問題の形式は1つの出題テーマに関して4~5つの正解もしくは誤りの文章のうち、正解の文章のみが含まれた選択肢を選ぶものとなっています。
どれか1つの文章の正誤がわからなくても回答できる場合があるため、学識のような記述式と比較すると簡単な形式です。
出題分野は年によって変わるものもありますが、だいたい同じような傾向です。
15問のうち、
①材料特性:金属材料など
②材料劣化:腐食など
③溶接:溶接方法など
④高圧装置:タンク、熱交換器、塔など
⑤計測機器:圧力計、流量計、温度計、液面計など
⑥圧縮機
⑦ポンプ
⑧漏洩防止:シール、パッキン、ガスケットなど
⑨計装、制御:各制御方法など
⑩安全・信頼性管理:HAZOP、フェーズ理論、特性要因図など
⑪⑫⑬⑭保安防災設備・運転管理:安全装置、緊急遮断装置、フレアースタックなど
⑮設備診断:非破壊試験など
大まかには以上のような内訳であることが多いです。
勉強する前からこれら全ての分野に精通している人はいないでしょうから、問題の形式が簡単だからといって油断はできません。
また、検定講習で講師がたまに出題される箇所を漏らすことがあるらしいので、SNSやネット掲示板等で情報共有するのもアリです。
以下に検定試験で過去に出題された内容や出題されやすそうな内容をまとめました。
材料特性
毎年1問、金属材料の特性が主として出題されています。
学識の材料特性の出題範囲とほぼ被っているので、学識でしっかり勉強しておけば特に対策は必要ないでしょう。
下の記事で学識の材料特性・材料劣化について解説しています。
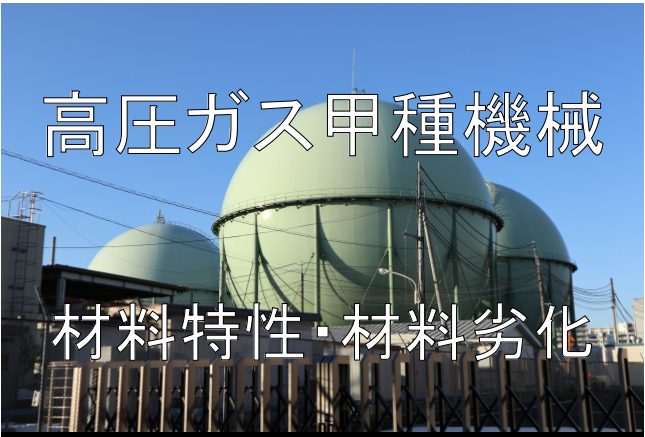
材料劣化
毎年1問、腐食について主として出題されています。
同様に学識の材料劣化と出題範囲が被っています。
溶接
毎年1問、溶接に関する内容が出題されています。
機械系の業種であればなじみ深いと思いますが、化学系の業種は実務で学ぶことがなかなかないので難しい分野かもしれません。
アーク溶接
被覆アーク溶接
被覆アーク溶接棒と被溶接部との間にアークを発生させて溶接を行なう方法です。
被覆アーク溶接棒は金属の心線とその周囲を覆う被覆材(フラックス)で出来ています。
フラックスは
・ガス発生剤・・・アーク及び溶接部をガスで被覆して空気の侵入を防止する。
・アーク安定剤・・・交流電源の場合のアーク再点弧を容易にし、アークを安定維持する。
・脱酸剤・・・溶融金属中に侵入した酸素をスラグとして除去する。
・合金添加剤・・・溶接金属の金属成分を微調整する。
などの成分が含まれています。
ティグ(TIG)溶接
タングステン電極と被溶接部の間にアークを発生させて、電極、アーク、溶接部を不活性ガスで覆って溶接する方法です。
tungsten inert gas weldingの略でTIG溶接と呼ばれます。
鋼鉄の溶接では、アークが安定する直流棒マイナスが使用されます。
その一方で、アルミニウムやアルミニウム合金の溶接では強固な酸化被膜を破壊するために交流電源が使用されます。
交流電源を使用すると、母材表面の酸化被膜上を陰極点が走り回り、陰極点の高熱により酸化被膜を破壊して溶接できる面にすることができます。これをクリーニング作用といいます。
サブマージアーク溶接
散布した粒状のフラックスの中にワイヤーを送給し、ワイヤー先端と母材の間にアークを発生させて溶接する方法です。
スパッタ、ヒューム、アーク光が過剰なフラックスに覆われて外部に出るのを抑えられることが特徴です。
ガスシールド消耗電極式アーク溶接
自動的に供給されたワイヤーの先端と母材との間にアークを発生させ、アークと溶接金属をガスで覆いながら溶接を行なう方法です。
ガスの種類によって、
・ミグ(MIG)溶接:metal inert gas welding 不活性ガスを使用。
・マグ(MAG)溶接:metal active gas welding 炭酸ガス、あるいはアルゴン+炭酸ガスを使用。
2種類に分けられます。
プラズマアーク溶接
アーク周囲を冷却すると、アーク中心は電流を維持するために緊縮し、より高温(2~5万℃)になる熱的ピンチ効果を利用して溶接を行なう方法です。
I開先の片側1パス突合せ溶接で、アークを裏側まで貫通させて溶接を行なう場合には、キーホール溶接と呼ばれることもあります。
ろう接
ろう接とは母材よりも低い融点をもつろう材を溶融させて接合させる方法です。
ろう材の融点により、
・ろう付け
・はんだ付け
に分けられています。
また、アルミニウム合金やステンレス鋼の熱交換器は真空ろう付けと呼ばれる方法で製造させることもあり、高圧ガス設備では多く使用されています。
溶接施工技術
溶接施工管理
・焼なまし
溶接後に溶接部周りに生じる残留応力を除去、緩和するための熱処理です。
溶接部およびその近傍は端部を除き、高温から室温になるときに熱収縮により引張応力が残留します。
この残留応力は靭性の低下や応力腐食割れの原因となることがあるため、一定以上の厚みを超える材の溶接部は応力除去焼なましが必要とされています。
詳しくは学識の材料特性記事で解説しています。
低温割れ
低温割れは金属中の水素拡散や溶接残留応力によって起こることが多く、高張力鋼、低合金鋼で生じやすいです。
通常はある時間経過してから発生するため、溶接部の検査を行なう際には24~48時間程度経ってから行なう必要があります。
高温割れ
高温割れはオーステナイト系ステンレス鋼やアルミニウム合金の溶接で生じやすく、特にアルミニウム合金ではクレータ部で生じやすいです。
溶接金属の成分に起因して割れが生じ、低温割れと違って溶接直後に発生します。
高圧装置
プラントで使用される各種高圧装置が毎年1題出題されています。
どの装置が出題されるかは年によって異なるため、ヤマが張りにくい分野です。
塔
蒸留塔
蒸留塔は多成分系の混合溶液を、その各成分の揮発性の違いを利用して使用目的に応じた成分に分離することを目的としています。
運転圧力は、常圧、減圧(大気圧以下)、高圧など成分と目的に応じて様々です。
吸収塔
吸収塔は気体と吸収液を接触させて気体中の成分を吸収液に溶解させる操作を行ないます。
用途としては、
・ガスの精製
・有用物質の回収
・有害成分の除去
などが挙げられます。
抽出塔
抽出塔は原料に含まれるある成分を抽出剤を用いて抽出分離することを目的としています。
抽出は多成分からなる原料の各成分の溶剤に対する溶解度の差を利用して分離しており、蒸留や蒸発では分離困難な原料に対して使用することが多いです。
吸着塔
吸着塔は流体と固体の接触界面に特定の成分が選択的に濃縮される現象を利用して分離することを目的としています。
吸着剤は内部表面積が大きい多孔質な物質が選定されることが多いです。
槽
球形貯槽
球形貯槽は単殻式と二重殻式の2種類あります。
・単殻式
天然ガス、都市ガスなどの圧縮ガス、あるいはプロパン、ブタンなどの液化ガスを常温高圧で大容量貯蔵するのに適しています。
近年は単殻式に高張力鋼が広く使用され、球面状にプレス成型した後、溶接で接合して球形とし赤道部に支柱を取り付けて全体を支持しています。
・二重殻式
低温液化ガスを大容量貯蔵するのに適しています。
熱交換器
各種類の熱交換器の特徴が出題されることが多いです。
多管円筒形熱交換器
熱交換器として最もよく使用される形式です。
互いに熱交換をする2流体が管板に取り付けられた多数の伝熱管内と胴側をそれぞれ流れ、伝熱管を通して熱交換を行ないます。
二重管式熱交換器
要求される交換熱量が小さい場合には二重管式熱交換器がよく使用されます。
分類として、
・Uチューブ式
・グランド式
・溶接式
などがあります。
よく使用されるUチューブ式では二重管とグランドから構成され、外管と内管をそれぞれ熱交換する流体が流れ、内管を通して熱交換を行ないます。
グランド部分が取り外しできるため清掃や点検は容易ですが、この部分から外管側流体が漏洩する可能性があります。
したがって、外管側にはなるべく冷却水などの危険性のない流体を流すようにします。
プレート式熱交換器
波形模様のプレートをガスケットを介して多数重ね合わせて、プレート間を1枚おきに高温流体と低温流体を流して熱交換する形式です。
プレート式熱交換器の利点として、
・熱伝達率(境膜伝熱係数)が大きく、同じ交換熱量で考えると装置の小型化が図れる
・分解、組立が容易であり清掃しやすい
・プレートを追加して処理能力を容易に変えられる
・滞留液量が少ない
などが挙げられます。
空冷式熱交換器
冷却媒体が空気である熱交換器です。
空気は熱伝導率、比熱が低いため、これを補うために伝熱管外側にフィンを設けて伝熱面積を大きくしています。そのため、エアフィンクーラーと呼ばれることもあります。
蒸発器
液化ガスを強制的に気化させてガスとして使用する目的で設置されます。
熱源により、
・温水式
・蒸気式
・空温式
に分けられます。
この中でも空温式蒸発器は特別な熱源を必要としないメリットはありますが、他の蒸発器と比較して設置面積が大きくなるデメリットがあります。
高圧ガス容器
高圧ガスの試験で出題される"高圧ガス容器"とは、高圧ガスを充てんするための入れ物で、移動することができるもののことをいいます。
継ぎ目なし容器
過去に出題された形式は、
・マンネスマン式・・・継ぎ目なし鋼管の両端を鍛造で成型加工したもの
・エルハルト式・・・鋼塊やアルミニウム合金塊を押出しなどで成型加工したもの
などがあります。
溶接容器
鋼板を冷間加工で成型し溶接により接合したもので、主に蒸気圧の低い液化ガス用に使用されています。
最近では軽量化対策として高張力鋼やアルミニウム合金などが使用されています。
超低温容器
容器自体は溶接容器と同様の方法で製造されますが、内槽と外槽の2槽に分け、その間に断熱材を積層して10Pa程度まで真空引きをしています。
内槽の材料は低温脆性を起こさないよう、一般的にオーステナイト系ステンレス鋼が使用されています。
可搬容器
内容積の違いにより大・中・小の3種類に分類され、可搬中容器を数本から数十本単位で枠組みしたものをカードルといいます。
刻印・表示
高圧ガス容器には高圧法により定められた刻印をしなければなりません。
容器外面の塗色(容器表面積の1/2以上)
・黒色:酸素ガス
・赤色:水素ガス
・緑色:液化炭酸ガス
・白色:液化アンモニア
・黄色:液化塩素
・褐色:アセチレンガス
・ねずみ色:その他の種類の高圧ガス
容器外面への表示
・充填することができる高圧ガスの名称
・充填することができるガスが可燃性ガス、毒性ガスの場合は
各ガスの性質を示す文字「燃」、「毒」
・所有者または容器管理業務受託者の氏名または名称、住所及び電話番号
管・管継手
配管設計上の注意
重力に対する考慮
配管系は圧力、重量及びその他の負荷荷重により発生する長手方向応力が許容応力値に収まるよう適切なサポートを設けなければなりません。
重量による荷重としては、
・輸送される流体
・試験流体
・雪及び氷の荷重からなる変動荷重
・配管部品
・保温保冷剤
・計装品
など、配管にかかる永久荷重と変動荷重を両方考慮する必要があります。
熱膨張・熱収縮に対する考慮
配管系は内部流体の流れにより流体温度とほぼ同じ温度となるため、熱膨張や熱収縮が発生します。
熱伸縮により配管系に発生する応力は、熱変位合成応力が許容応力範囲に収まるよう配管ルートやサポートを設定しなければなりません。
熱伸縮の吸収対策として、
・配管系の形状への配慮
・伸縮管継手の使用
・コールドスプリングの使用
が挙げられます。
コールドスプリングとは配管組立時にあらかじめ配管系に熱変位方向とは逆向きの変形を与えておき、最高(最低)運転温度における変位を軽減させる方法です。
振動に対する考慮
・圧力脈動に対する考慮
配管長さを変えたり、オリフィスを挿入するなどにより気柱振動との共振を避けます。
・機械振動に対する考慮
配管系の固有振動との共振を避けるようにサポートの指示間隔を調整します。
固定バンドなどを用いて配管系を強制的に拘束します。
かなり細かい内容ですが、以前に出題されたことがあります。
エルボレス配管
エルボレス配管では曲げ箇所が減肉するため、管内圧に対する強度を確保するために初期の管肉厚を厚めにしておく必要があります。
計測機器
毎年1題出題されていますが、出題範囲が非常に広く、勉強するのが難しい分野です。
キーワードだけうまく覚えて乗り切りたいところです。
温度計
バイメタル温度計
熱膨張率の異なる2種類の薄い金属を貼り合わせたものをバイメタルといい、温度が上昇すると熱膨張率の小さい方へ曲がることを利用して温度を測定します。
液体充満圧力式指示温度計
ブルドン管及び感温部からなる系内に液体を充満し、感温部内の液体の温度によって膨張、収縮した結果生じる圧力変化をブルドン管に伝えて指針を動かします。
熱電温度計
2種類の導体を電気的に接続して作成した回路を熱電対といい、この回路の両端には温度差にほぼ比例した熱起電力が発生します。
これをゼーベック効果といい、この効果を利用して温度を測定しています。
抵抗温度計
金属の電気抵抗は温度上昇によって変化するため、金属線の電気抵抗を測定することにより温度を測定します。
金属としては白金、ニッケル、銅などが使用されていますが、最も適しているのは白金です。
圧力計
U字管圧力計(マノメータ)
ガラス管をU字型に曲げたものに液体を入れて、液柱の高さの差Δhを読み取ることで圧力差Δpを測定します。
液柱の高さの差Δhと圧力差Δpはベルヌーイの定理から
$$Δp=ρgΔh$$
と表されます。
U字管に封入する液体は、一般に水か水銀が使用されます。
重錘式圧力計
分銅式圧力計、浮遊ピストン式圧力計とも呼ばれます。
ラムに重錘を載せてハンドルを回すと、ピストンが油を圧縮してラムと重錘が浮き上がります。
測定する圧力と釣り合ったところでのラム下端にかかる圧力は、
$$p_{g}=\frac{mg}{A}$$
pg:ラムにかかるゲージ圧[Pa]、m:ラム及び重錘の質量[kg]
A:ラムの有効受圧面積[m2]
となります。
精度が高く、ブルドン管圧力計を検査、校正するための圧力基準器に使用されます。
ブルドン管圧力計
ブルドン管とは断面が楕円や平円形などの金属管を円弧上に曲げて、その一端を圧力を導入する部分に固定して他端を密閉して自由に動けるようにしたものです。
このブルドン管に圧力が加わると、全体が一直線になるように外側に向かって変形します。
ただし、この変位は極めて小さいため、ピニオン・セクタなどの拡大機構で拡大して、目盛版上の指針で圧力を読み取ります。
隔膜式圧力計
ブルドン管圧力計に隔膜部(ダイヤフラム)を設けて、隔膜部とブルドン管の間にシリコーンオイルなどの液体を封入したものです。
ダイヤフラムで受けた圧力を、封入液を圧力媒体としてブルドン管に伝達して変位させることで圧力を検出します。
測定流体がブルドン管に入らないため、隔膜式圧力計は腐食性流体、高粘度流体、スラリーなどの固形物が混入した流体、凝固しやすい流体などの特殊流体に使用されます。
過去には"ブルドン管を使わずに"という引っ掛け問題が出ていますので注意しましょう。
流量計
差圧式流量計
管路内にオリフィスやベンチュリ管などの絞り機構を設けて、流量に応じた差圧を測定して流量を求めます。
オリフィス流量計
絞り機構で最もよく使用されるのが同心オリフィスタイプです。
ただし、他の絞り機構と比較して圧力損失が大きく、オリフィス内径部分のエッジが摩耗すると測定誤差が生じるため、固形物の混入は避ける必要があります。
ベンチュリー管
オリフィスに比べて圧力損失が小さく、沈殿物がたまりにくい利点があります。
したがって、異物を含む流体やできるだけ圧力損失を小さくしたい場合に使用されます。
ベンチュリー管については以下の記事で解説しています。
-
【ベンチュリー管】を解説:流路の拡大縮小による流量測定
上図のようにゆるやかな縮小部と拡大部を持つ管をベンチュリー管と呼びます。ベンチュリー管は動圧と静圧の異なる箇所を作り出し、各々の箇所の静圧差を測定することで流速及び流量を測定できます。
続きを見る
面積式流量計
鉛直に置かれたテーパ管の中を下から上に流体を流します。
テーパ管内にはフロートが設置されており、流量の変化に応じて上下に移動するようになっています。
このフロートの動きを検出して流量を求めています。
渦流量計
流れに垂直に柱状物体を挿入すると、その物体の両側から互いに逆回転の渦が発生します。
これをカルマン渦といいます。
このカルマン渦列の周波数fと流速uとの間には、
$$f=\frac{St・u}{D}$$
St:ストローハル数、D:渦発生体の流れに対する幅
上のような関係があるため流速を算出することができます。
コリオリ式流量計
加振したチューブ内に液体を流すと、流入・流出側それぞれに反対方向のコリオリ力が生じてチューブがねじれます。
このねじれ角は配管内の質量流量に比例するため、ねじれ角を振動センサーにより位相差信号として検出することで流量を測定します。
測定原理についてひっかけ問題が出題されやすいので、他の測定原理と合わせて覚えておきましょう。
液面計
差圧式液面計
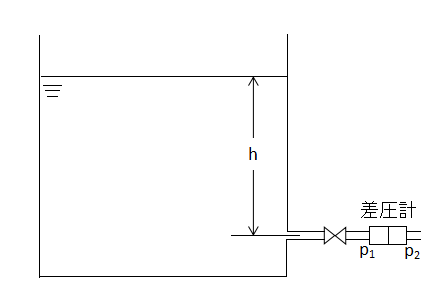
図のようなタンクに差圧式液面計を取り付けた場合、液面の高さh[m]は、
$$h=\frac{p_{1}-p_{2}}{ρg}$$
p1:高圧側圧力[Pa]、p2:定圧側圧力[Pa]
ρ:液体密度[kg/m3]、g:重力加速度[m/s2]
となります。
また、差圧式液面計には
・ウェットレグ方式
・ドライレグ方式
・リモートシール型
などの種類があります。
ディスプレーサ式液面計
円筒状のディスプレーサを液中に浸すと、液中に沈む深さに比例して浮力を受けます。
この浮力による重力の変化を検出し、トルクチューブを用いてねじれ角を検出し液面・界面を測定します。
ガス濃度分析計
ガスクロマトグラフ
ある種の物質に対してガスがもっている物理的な親和力の大きさの違いを利用して、ガスを成分ごとに時間的に分離することでガス濃度を検出する方法です。
赤外線式分析計
測定対象の分子に関する赤外線吸収量を測定することによりその成分のガス濃度を測定する方法です。
圧縮機
毎年1問出題されています。
学識では記述式の問題が出題されていますが、学識で必要とされる知識と保安管理技術で必要とされる知識は異なることが多いため、学識とは別に勉強が必要です。
多段圧縮機
気体を高圧に圧縮する場合は、1段で圧縮するよりも多段で圧縮する方が1段当たりの圧縮比を小さく取ることができます。
また例えば2段圧縮機の場合に、1段目で圧縮した後に最初の温度まで中間冷却して2段目の圧縮を行なうと仕事の節約になります。
これは中間冷却を行なうことで、断熱圧縮から等温圧縮に近づくためです。
ターボ形圧縮機
ケーシングの段数
1つのケーシングの段数は主に軸の危険回転数によって制約を受けます。
段数が多い場合には複数のケーシングを使用します。
軸シール
代表的な軸シールとして、ラビリンスシール、オイルフィルムシール、メカニカルシール、ドライガスシール、カーボンシールがあります。
サージング
吐出し側の抵抗が大きくなると風量が減少し、逆流と圧力変動が発生して不安定な運転状態となります。
この現象をサージングといいます。
引っ掛け問題で出題されやすいので注意しましょう。
バイパスコントロール
圧縮機プラントの吐出し管路の途中にバイパス菅を設け、吐出し風量の一部を吸込み側へ戻すか大気放出することにより、サージング領域にある送風量での運転を可能とする方法です。
圧縮機自体の負荷は変わらないため、送風量減少による動力の減少効果はありません。
遠心圧縮機の速度制御
遠心圧縮機の風量q、ヘッドH、動力L、回転数Nについて、圧縮比があまり大きくなければ近似的に
$$q∝N$$
$$H∝N^{2}$$
$$L∝N^{3}$$
上のような関係が成り立ちます。
ターボ形圧縮機の振動
ターボ形圧縮機はインペラが高速回転するため、振動には特に注意を払う必要があります。
例えば心ずれにより振動が発生した場合は、振動の主周波数fは回転数をNとすると、
f=N,2N,3Nとなります。
容積形圧縮機
ピストンロッドパッキン
ピストンロッドのシリンダ貫通部の気密性を高めるためにシールします。
種類として
・セグメントタイプ
・ラビリンスタイプ
があり、最も広く使用されているのはセグメントタイプです。
油圧の異常
油圧が異常に上昇、低下する原因としては、潤滑油ポンプ、フィルタ、リリーフ弁の異常や油温の異常などがあります。
温度の異常上昇
ある段の温度が異常に上昇する原因としては、
・後段の吸込み弁、吐出し弁の不良による逆流
・前段冷却器の能力低下
・圧縮比の増加
などがあります。
温度の異常低下
ある段の温度が異常に低下する原因としては、
・前段冷却器の過冷却
・圧縮比の低下
・シリンダの過冷却
などがあります。
ポンプ
毎年1問出題されています。
ポンプに関しても同様に、学識で必要とされる知識と保安管理技術で必要とされる知識が一部異なります。
キーワードを中心に覚えていきましょう。
ポンプ揚程
各種ポンプの揚程が出題されることがあります。
・遠心ポンプ:単段で10~550m、多段では4000m程度。
・斜流ポンプ:単段で5~60m、多段では150m程度。
・軸流ポンプ:1~8m程度。
粘性流体による効率低下
流体の粘性が高いとポンプの効率が低下することがありますが、ポンプの種類によります。
・遠心ポンプ:効率低下が大きい。
・往復ポンプ:効率低下はほとんどない。
・回転ポンプ:効率低下は小さい。
キャビテーションの発生防止
キャビテーションの防止対策として、以下のようなものがあります。
・ポンプの据え付け位置をできるだけ下げる。
・ポンプの回転数を下げる。
・吸込み液面を上げる。
・吸込み液面圧力を上げる。
サージング
サージングは圧縮機だけに起こるものではなく、ターボ形ポンプでも起こる可能性があります。
サージングを防止する方法として、
・羽根車や案内羽根の形状寸法を変えて特性を変化させる。
・放出弁などを使用してポンプ内の揚水量を増加させたり、回転数を変化させる。
・管路の残留空気を取り除き、管路断面積、揚液の流速抵抗を変化させる。
などがあります。
水撃作用(ウォーターハンマー)
停電等でポンプが急に停止したり、容量調節弁を急に開閉した場合に、管内の流速が急変すると液圧の激しい変化で管を鉄棒で叩いたような音が発生します。
これを水撃作用(ウォーターハンマー)といいます。
水撃作用の防止方法としては、
・吐出し配管内流速が遅くなるような管径を選定する。
・ポンプのフライホイール効果を大きくし、急にポンプが止まっても回転速度が徐々に低下するようにする。
・吐出し配管に空気弁を設ける。
などが挙げられます。
並列・直列運転
1台のポンプで流量、揚程が不足する場合は複数台で運転することがありますが、特性には注意が必要です。
同一特性のポンプの並列運転
2台並列運転時の吐出し量は1台運転時の2倍となります。
もし並列運転から単独運転に切り替える場合は、遠心ポンプでは1台当たりの所要軸動力が並列運転時より大きくなるので注意が必要です。
特性の異なるポンプの並列運転
特性の異なるポンプを2台並列運転する場合に、配管集合後の吐出し弁を絞って流量調整すると片方のポンプの吐出し量がゼロに近くなることがあります。
このような運転は避けなければいけませんので、ポンプの流量特性と運転条件はしっかり確認しましょう。
また、試験にも出題されやすい内容です。
直列運転
2台直列運転は揚程を増大させる場合に使用されます。
遠心ポンプの場合、直列運転時の1台当たりの所要軸動力は1台単独運転時よりも大きくなるので注意が必要です。
漏洩防止
毎年1問出題されています。
他の分野に比べれば簡単だと思います。
ガスケット
ガスケット設計締付け応力・ガスケット係数
ガスケットが接触面に密着して流体の漏洩を防ぐために必要な力をガスケット締付け力といいます。
このガスケット締付け力をガスケットの有効面積で割ったものをガスケット設計締付け応力といいます。
また、流体の漏洩を防止するために必要な圧縮力である最小必要残留圧縮応力と内圧の比をガスケット係数といい、ガスケットの材質と構造によって決定されます。
熱交換器のガスケット
熱交換器のノズルやシェルカバーのフランジガスケットには、ジョイントシート、メタルジャケットガスケット、金属リングガスケットなどが使用されています。
ホットボルティング
金属リングガスケットは締付けによる変形後の復元力が小さいため、高温配管に使用するときは高温増し締め(ホットボルティング)を行ないます。
金属リングガスケットは頻出項目ですので必ず覚えておきましょう。
バルブの弁座漏れ
バルブの弁座漏れチェックはJISに規定があります。
試験流体は水と空気で、それぞれに許容される漏れ量が決められています。
ボルトの締付け管理
ボルトの締付け方法は、
・手締め法:スパナ等で人力で締め付ける方法。
・トルク法:トルクレンチや油圧レンチを使用して締め付ける方法。
・回転角法:分度器や電気的な検出器を使用してナットの回転角を確認しながら締め付ける方法。
・テンション法:ボルトテンショナを使用して締め付ける方法。
・伸び測定法:ボルトの伸びを超音波軸力計や伸びゲージなどで測定しながら締め付ける方法。
などが挙げられます。
往復圧縮機の軸封装置
ピストンロッドパッキン
ピストンロッドはパッキンとのわずかなすき間を介して往復運動しているため、ダストや錆が存在するとピストンロッドの外周に傷がつきやすいです。
したがって、ダストの付着防止、焼き付き、かじり防止のためにこの部分へは注油し、なおかつ摩耗低減の為に冷却が必要です。
遠心圧縮機の軸封装置
遠心圧縮機の軸封装置には、
・ラビリンスシール
・メカニカルシール
・オイルフィルムシール
・ドライガスシール
などが使用されます。
ラビリンスシール
構造上、圧縮機内のガスが外に漏れることは避けられません。
したがって、圧縮機内のガスが大気中に漏れても問題ない場合はラビリンスシールが採用されることがあります。
メカニカルシール
メカニカルシールはポンプ軸に取り付けられた回転環と、ケーシング側の固定環でポンプ軸に垂直な面を形成するタイプの端面密封方式です。
内部流体の漏洩をほぼ完全に止めることができるため、可燃性、毒性流体に使用されます。
オイルフィルムシール
オイルフィルムシールは軸とわずかなすき間を有する2つのリングをはめ込み、そのリング間に内部ガス圧より高い圧力で油を供給し、油膜を形成してガス漏れを防ぎます。
水素ガスやアンモニアガスなどの大気中への漏れが許容されないガスに使用されます。
ドライガスシール
従来のメカニカルシールでは周速が130m/s以上になると適用が難しい問題がありました。
そこで、ドライガスシールでは摺動面に動圧溝を設けてシール面を非接触とすることで周速が速くても対応できるようにしています。
非接触であるためシール面の摩耗はほとんど発生しませんが、ガスの漏洩は若干生じます。
ポンプの軸封装置
・往復ポンプ
ピストンロッドパッキンとしてグランドパッキンが使用されます。
グランドパッキンはわずかな漏れが許容される場合に使用されます。摺動部とパッキンとの接触によりシールするため、摩擦によりパッキンが摩耗し漏れが大きくなります。
そのため、定期的にグランドパッキンの締め直しを行なう必要があります。
・遠心ポンプ
グランドパッキンやメカニカルシールが使用されます。
計装・制御
毎年1問出題されています。
実務でプラントの運転に携わっている人は特に勉強する必要がないかもしれません。
それくらいどの制御方法もプラントでは当たり前に使用されています。
フィードバック制御
プロセスに外乱が入って目標値と制御量の間に偏差が生じると、操作量を変えて制御量が目標値と一致するように制御する方法です。
フィードフォワード制御
プロセスに外乱が入った場合に、その影響が制御量に現れる前にそれを打ち消す操作を加える方法です。
フィードフォワード制御だけでは目標量と制御量が一致したか確認することはできないため、通常はフィードバック制御と組み合わせて使用します。
フィードバック制御との引っ掛け問題でよく出題されています。
カスケード制御
ある調節計の出力値により他の調節計の目標値を制御する方法です。
流量や圧力、温度に変動があってもなるべく他のプロセス値に影響が出ないよう制御できるため、プロセスの安定性が向上します。
シーケンス制御
あらかじめ定められた操作手順に従って次々と自動的に操作を行なう方法です。
プラントのスタートアップ・シャットダウンなどの非定常運転を自動化するために使用されることが多いです。
制御動作
オンオフ動作
調節弁を全開または全閉にする方法です。
細かな制御量の調整ができず、制御量が増加したり減少したりする持続的振動(サイクリング)が発生することがあります。
比例動作(P動作)
操作量を現在の制御偏差に比例して変化させる方法です。
比例動作の強さは比例帯という用語で表されます。
比例帯が狭いほどわずかな偏差で調節弁は全開・全閉になり動作が強くなります。
また、比例帯の逆数を100倍したものを比例ゲインといいます。
同様に比例ゲインを大きくするほどわずかな偏差で大きな操作量を出力し、だんだんとオンオフ制御に近づきサイクリングを起こします。
比例帯と比例ゲインの引っ掛け問題がよく出題されています。
積分動作(I動作)
操作量が偏差の時間積分値に比例する方法です。
積分時間が短いほど積分動作が強くなり、偏差が存在する限り操作量が変化し続けます。
積分動作は比例動作で生じるオフセットを消すことができるため、通常は比例動作と組み合わせてPI動作として使用されます。
微分動作(D動作)
偏差の変化速度に比例して操作量を変える方法です。
微分動作をうまく活用すれば、制御量が目標値に到達するまでの時間を短くでき、むだ時間を減らすことができます。
微分時間が長いほど微分動作が強くなります。
調節弁の流量特性
調節弁の弁開度と流量の関係を流量特性といいます。
代表的な流量特性として、
・リニア特性:最も好ましい流量特性。
・イコールパーセント特性:系全体の圧力配分が不明な場合に選定される。
・クイックオープン特性:オンオフ弁として使用するときに選定される。
などが挙げられます。
フール・プルーフ
人がミスしないように配慮すること及びミスを犯しても機器の安全性を保持することをフール・プルーフ(fool-proof)といいます。
フール・プルーフの例として、
・スイッチやボタンの色を通常時用と緊急時用で区別する。
・緊急時にのみ操作するボタンにカバーを付ける、二段操作にする。
・インターロックシステムを導入する。
等が挙げられます。
フェール・セーフ
機器・設備に異常や故障が生じたときでも装置が安全な状態になるよう配慮することをフェール・セーフ(fail-safe)といいます。
フェール・セーフの例として、
・弁の駆動用電源や空気が喪失した場合でもプラントが危険な状態にならないよう弁の駆動部方式を選定する。
・熱電対温度計からの信号線が断線した場合に、加熱操作にならないよう変換器からの出力信号を上限に振り切れるようバーンアウト機能を設定する。
・警報機について、正常時励起状態で運用する。
等が挙げられます。
冗長システム
万一機器が故障してもシステムに影響がないよう、機器を複数台用意しておくことを冗長化といいます。
機器を並列に多重化する方法や故障した場合に機器を切り替える方法など様々な冗長系があります。
安全・信頼性管理
毎年1問出題されています。
リスク解析手法はアルファベットの略語だらけで紛らわしいですが、引っ掛け問題としてよく出題されていますので正確に覚えておく必要があります。
HAZOP(Hazard and Operability)
連続系とバッチ系で2種類の手法があります。
いずれも手法も、プロセスパラメータや操作手順の正常な状態からのずれを想定してハザードを特定します。
FTA(Fault Tree Analysis)の頂上事象の選定に便利です。
What-if
「もし・・・したら、どうなる。」という質問を繰り返すことで設備・運転面でのハザードを特定し、それに対する安全対策を検討することによりシステムの安全化を図る方法です。
複数の事象の組み合わせを想定することも可能です。
FTA(Fault Tree Analysis)
対象とするシステムの危険事情を頂上事象として設定し、頂上事象の原因を機器・部品レベルまで掘り下げて、原因と結果を論理記号で結びつけツリー状に表現する論理図解析手法です。
各々の機器・部品の故障確率を与えることで頂上事象の発生確率を解析するため、演繹的な解析手法とされています。
要因相互の因果関係や各要因の事故に対する寄与の度合いを知るのに便利です。
ETA(Event Tree Analysis)
1つの引金事象がどのように拡大していくのかを解析し、最終的に到達する災害事象をツリー状に表現する帰納的解析手法です。
小規模トラブルの波及拡大過程を解析するにに便利です。
FMEA(Failure Mode and Effects Analysis)
システムを構成する機器に着目し、その機器に考えられる故障モードをとりあげ、故障がシステムに及ぼす影響と安全対策を解析する要素解析手法です。
FTAを行なう際に頂上事象に関係する構成基本事象の選択に便利です。
ハインリッヒの法則
災害データを収集して分析すると、
・重大災害:1件
・中程度の災害:29件
・無災害事故(ヒヤリを含む):300件
このような比率(1:29:300)になることをハインリッヒの法則といいます。
この法則から、ヒヤリの段階で危険な要因を排除しておくことは重大災害の発生の予防対策の1つとして重要であると言えます。
特性要因図
問題とする特性とそれに影響していると思われる要因との関連を整理して、魚の骨のような図にまとめたものを特性要因図といいます。
事故原因を分類整理し、どこに管理の重点を置いたらよいかを知るのに便利ですが、要因相互の因果関係を明確に把握することはできません。
4M
事故や災害は人、物、環境の複合的な要因が複雑に絡み合って起こることが多いです。
そこで、事故の原因分析や対策検討の際に人間工学の面から要因を、
・MAN(人)
・MACHINE(機械)
・MEDIA(媒体または環境)
・MANAGEMENT(管理)
の4つのジャンル(4M)に整理することで原因の本質を捉えやすくなります。
フェーズ理論
人間の意識レベルを5段階のフェーズに分けた考え方をフェーズ理論といいます。
・フェーズ0:無意識、失神
・フェーズⅠ:意識ぼけ
・フェーズⅡ:リラックス状態
・フェーズⅢ:積極的活動、意欲的
・フェーズⅣ:過緊張、情動興奮
どのフェーズがどの意識レベルに対応するかを問う問題が出題されることが多いです。
頻出ですので必ず覚えましょう。
保安防災設備・運転管理
これらの分野から毎年4問ほど出題されています。
出題範囲が広く、勉強するのがかなり難しい分野です。
問題のレベルは、勉強せずとも常識でわかる問題から、細かい数字を問う問題まで様々で年によって当たり外れがあります。
ある程度割り切って得意なところだけ覚えるのも手かもしれません。
保安電力
常用発電の原動機はスチームタービンや最近ではガスタービンが使用されています。
非常用発電の原動機はディーゼル機関、ガソリン期間などの内燃機関が主流となっています。
スチームタービン
スチームの利用形態によりタービンの形式が分けられます。
・復水タービン
・抽気復水タービン
・抽気背圧タービン
・背圧タービン
スチームタービンは主に常用発電設備として使用されます。
事業所で使用するスチームに余剰が出る場合や、夏場と冬場での必要スチーム量が異なりますので、様々なケースを検討する必要があります。
ガスタービン
燃焼ガスの利用形態により2種類に分けられます。
・オープンサイクル:急速始動が可能でピーク負荷用に適している。
・クローズドサイクル:始動に時間を要する。比較的利用率の高いところに適している。
蓄電池設備
非常用電源には一度放電すると再使用できない一次電池ではなく、充電を行なえば繰り返し使用できる二次電池が採用されます。
二次電池は鉛蓄電池やニッケル・カドミウムアルカリ蓄電池などが使用され、電池の容量は設備を安全に停止できる保安面から決定します。
燃料電池
代表的な燃料電池は、負極に燃料となる水素、正極に酸化剤として空気中の酸素を供給し、水素と酸素の酸化反応により電気を取り出します。
無停電電源設備
緊急安全装置などの瞬時の停電も許されないものには、非常用電源として無停電電源設備(UPS)または蓄電池から電源を供給し、常用の電源が停電してもこのような装置には連続して電力を供給できるようにします。
UPSは設備が安全に処置できる時間として、30分間以上供給するものとして蓄電池の容量を決定します。
設問では非常用電源切り替え時に瞬断がある、もしくは一時的な電圧の低下があるといった引っ掛け問題が出題されやすいです。
接地計画
静電気災害の防止
・配管中の流体の流速を低下させることにより静電気の発生を抑制できます。
・静電気を除去するために導体に接地を施すことで、帯電電位の低下や緩和が期待できます。また、金属導体を同電位にするために、電線などで複数の金属を接続することをボンディングといいます。
・石油製品などの可燃性液体はタンクへの流入時に摩擦により静電気が発生し、表面に電荷が帯電します。この電荷は時間とともに減少するため静置すればよいですが、液体の種類や容積によって必要な静置時間が異なります。
例えば、原油や重油は体積抵抗率が低く、静電気が帯電しにくいため静置時間が短くて済みます。
安全装置
安全弁
安全弁とはバルブの入口側の圧力が上昇してあらかじめ定められた圧力になったときに、自動的に作動して弁体が開き流体を外側に排出し、圧力が所定の値まで降下すれば再び弁体が閉じる機能を持つバルブのことです。
種類として、
・ばね式:揚程式安全弁、全量式安全弁
・おもり式
などがあります。
揚程式安全弁:リフトが弁座口の径の1/40以上1/4未満で、弁体が開いた時の流路面積の中で弁座流路面積が最小となる。
全量式安全弁:弁座流路面積が弁体と弁座との当たり面より下部にあるノズルののど部の面積より十分大きなものとなるリフトが得られる。
揚程式安全弁と全量式安全弁のひっかけ問題が多いので覚えましょう。
破裂板
破裂板(ラプチャーディスク)は系内が過剰圧力になった場合に破裂することで内部の流体を放出し圧力を下げるものです。
安全弁と比較して、
・構造が単純で吹出し抵抗が小さい。
・内部圧力を降下させるまでの時間が極めて短い。
・取り扱い、点検が容易であり弁座漏れがない。
などの特徴があります。
逃し弁
逃し弁はばね式安全弁と同様の機能ですが、主として液体の圧力上昇を防止するために使用されるものです。
緊急遮断装置
遮断弁
遮断弁はダイヤフラム、ピストンなどに空気圧、油圧、電気またはばね(手動)を動力として使用し、弁を急速に開閉する構造となっています。
作動形式
貯槽用の緊急遮断装置は遠隔操作できるようにしておかなければなりません。
また、遮断操作を行なう場所は貯槽の外面から5m以上(コンビ則の適用を受ける場合は10m以上)離れた位置である必要があります。
遮断特性
・検査
緊急遮断弁は定期的に弁座漏れ検査、作動検査を行なう必要があります。
・ウォーターハンマー
長距離配管の場合には弁が急速に閉まるとウォーターハンマーが発生する可能性があるため、弁の閉止時間が短すぎないように配慮する必要があります。
冷却装置
液化ガス貯槽について
液化ガス貯槽の温度上昇防止対策について過去に出題されています。
・冷却用水噴霧装置、散水装置
貯槽の表面積1m2当たり5L/min以上の水量が必要です。
・消火栓
当該貯槽の外面から40m以内に貯槽に対していずれの方向からも放水できる消火栓を設ける必要があります。
・水源の容量
水噴霧装置などは同時に放射を必要とする最大水量を30分間以上連続して供給できる水源に接続しなければなりません。
ガス漏洩検知警報設備
接触燃焼式
白金線コイルをベースにした検知素子と不活性物質をコーティングした補償素子及び一対の固定抵抗から構成され、ホイールストンブリッジが組まれています。
可燃性ガスが微量でも存在すると白金の検知素子表面で燃焼反応が起こり白金コイルの電気抵抗値が増大します。
可燃性ガスの存在しない雰囲気下ではブリッジに常時300~400mAの電流が流れ、電気的平衡を保っていますが、可燃性ガスにより白金コイルの抵抗値が増加すると電気的平衡が崩れて電圧出力が発生することでガスを検知します。
半導体式
焼結された金属酸化物の半導体をヒータ電源を使用して100~500℃に加熱しておきます。
この半導体に可燃性ガスの濃度が増加すると、金属酸化物の電気抵抗値がn形半導体は大幅に減少し、p形半導体は増加する現象を利用してガスを検出します。
半導体式では不活性ガスの他に可燃性ガス、毒性ガスなどほとんどすべてのガスを検知することができます。
定電位電解式
プラスチック製容器に隔膜、作用電極、対極を設置し、容器に電解液を満たした構造となっています。
あらかじめ2極間に酸化電位を与えておき、検知ガスが隔膜から侵入すると2極間に拡散電流が流れることを利用してガスを検出します。
一酸化炭素、硫化水素などの毒性ガスの測定に適しています。
赤外線式
赤外光線がガスセルの中を通過し、赤外センサに到達する際に炭化水素ガスによる赤外線吸収を測定して検知します。
炭化水素と赤外線を吸収する波長が異なる炭酸ガスとは干渉を起こしません。
また、赤外線式は接触燃焼式と比較して、被毒物が吸着することがないため感度変化をほとんど起こしません。
ガルバニ電池式
作用極、対極、電解液、ガス透過性隔膜により構成されています。
検知ガスが電解液中へ溶解すると溶存濃度に比例した還元電流が発生するため、この電流を測定してガス濃度を知ることができます。
例えば酸素ガス測定の場合は、作用極に白金、金などの貴金属、対極には鉛などの卑金属が使用されます。
電池系の問題は2極に使用する材質や反応する物質を入れ替えた引っ掛け問題が出題されやすいのでよく確認しておきましょう。
フレアースタック・ベントスタック
フレアースタック
フレアースタックは廃ガスを燃焼させて、安全かつ環境を汚染しないように大気中に放出する目的で設置されます。
種類としては、
・エレベーテッドフレアー:廃ガスを高所で焼却する。
・グランドフレアー:廃ガスを地上で焼却する。
の2種類に分けられます。
最近はエレベーテッドフレアーから発生する黒煙や明るさ、騒音が公害として取り上げられているため、安全性の高いグランドフレアーが使用され始めています。
燃焼炎の安定性
正常な燃焼状態では火炎が目に見える状態であり、このときは火炎はスタックの端面から浮き上がった位置で安定しています。
これを浮上りといいます。
黒煙発生の防止方法
黒煙発生の防止方法は、
・予混合バーナを使用する。
・スチームの吹込みを行なう。
・小バーナを多数使用する。
などがあります。
通常はスチーム吹込み方式が利用されています。
逆火防止
逆火防止方法は、
・ドライシール
・水封
・不活性ガスによるパージ設備
・フレームアレスタ:凝縮性ガスのない場合に適用。
などの方法が利用されています。
特に燃焼速度が大きい水素やアセチレンは逆火の恐れが大きいため注意する必要があります。
ベントスタック
ベントスタックには緊急時に移送したガスを放出するための緊急設備にかかわるものと、その他のものの2種類に分けられます。
それぞれのベントスタックの放出口の位置は、作業員が定常作業を行なうために必要な場所及び作業員が通常通行する場所の直下またがこれらの場所から所定の距離を取る必要があります。
・緊急用ベントスタック:10m以上
・その他のベントスタック:5m以上
除害のための措置
拡散の防止
・水溶性ガスが漏洩した場合は、水などの溶媒によって希釈しガスの蒸気圧を低下させます。
・漏洩した液化ガスの液面を吸着剤、吸収材、中和剤、気泡性液体、もしくは浮遊小球などで覆い、液化ガスの蒸発気化をできるだけ少なくする。
このあたりが過去に出題されています。
除害措置
・アンモニアまたはシアン化水素は燃焼設備(フレアースタック、ボイラーなど)で安全に燃焼させて除去します。
除害設備
・加圧式、動力式などによって作動できる除害剤散布装置または散水装置
例として、塩素の除害には消石灰を微粉化したものを散布する装置が挙げられます。
・ガスを吸引しこれを除害剤と接触させる装置
例として、塩素の吸収塔では苛性ソーダ水溶液や石灰乳が吸収水として使用されます。
運転中に起こりえる異常
引っ掛け問題として出題されやすいので、各異常がどういうものか正確に覚えましょう。
回転機器などの振動・異音の発生
圧縮機、ポンプなどの回転機械は部品に欠陥があれば振動や異音が発生しますが、部品に欠陥がなくてもサージングやキャビテーションの発生によって振動や異音が発生することがあります。
飛沫同伴(エントレインメント)
塔内の蒸気速度が速くなると、液滴が蒸気に同伴して上のトレイまで到達する現象のことです。 塔内のガス流速が速い場合に、トレイ上や充填物表面の液滴がガスに同伴し上段へ運ばれる現象をエントレインメント(飛沫同伴)といいます。 続きを見る
下記の記事で詳しく解説しています。
【エントレインメント(飛沫同伴)】を解説:蒸留塔の効率低下原因
溢汪現象(フラッディング)
塔内の蒸気流速が増加すると、トレイ上の液が降下できなくなり上段に運ばれる現象をフラッディングといいます。 充填塔の操作においてガス速度を速くし過ぎると、液が塔内を流下できなくなりガスによって持ち上げられてしまいます。この結果、塔底から液が出てこなくなり塔頂から液が溢れ出します。この状態をフラッディング(溢汪 いつおう)といい、フラッディングが始まる点をフラッディング点と呼びます。 続きを見る
下記の記事で詳しく解説しています。
【フラッディング(溢汪)】を解説:蒸留塔の運転上限
脈動(パルセーション)
トレイ上の液深が深い場合や蒸気流量が少ない場合に、蒸気がトレイのガス穴から断続的に吹き出すことで液面が脈動する現象をパルセーションといいます。
トレイの段効率が低下してしまうため、蒸気流量を増加させて適正な運転範囲にするのが望ましいです。
ブローイング
トレイ上の液浸が浅い場合に、ガス穴から吹き出す蒸気によって液が吹き飛ばされる現象をブローイングといいます。
同様に段効率が低下するため、液流量と蒸気流量のバランスを適正化する必要があります。
ウィーピングとダンピング
蒸気量が減少するとトレイのガス穴から液が漏れる現象をウィーピングといいます。
このウィーピングの液漏れ量がさらに激しくなるとダンピングと呼ばれます。
ウィーピングについては下記の記事で詳しく解説しています。
-
【ウィーピング】を解説:蒸留塔トレイからの液漏れ現象
棚段塔において、トレイの小孔(ガスの通り穴)から液が漏れる現象をウィーピングといいます。
ウィーピングが起こっても塔を運転することはできますが、トレイ上の液深が低くなり気液接触の効率が悪化してしまいます。続きを見る
加熱炉・反応器に起きる異常
加熱炉や反応器でスケールの付着などにより局部的に過熱状態になることがあり、その箇所をホットスポットと呼びます。
ホットスポットは周囲よりも輝度が大きく、ホットスポットが材質表面に形成されるとその部分の強度が低下して破損する恐れがあります。
設備診断
毎年1問出題されています。
出題内容を絞りやすく他の分野と比べると簡単です。
浸透探傷試験(PT)
試験体の表面の油脂を除去した後、
・浸透処理
・余剰浸透液の除去
・現像処理
・観察
の4つの工程で検査を行ないます。
試験体の表面に開口している微小な割れ、穴、巣などの肉眼では確認できない微細な欠陥を検出するのに広く使用されている方法です。
浸透探傷試験は金属に限らず、プラスチック、ガラス、セラミックスなどにも適用できます。
磁気探傷試験(MT)
試験体を磁化して欠陥部に生じた磁極により強磁性体の微粉末が付着することを利用して、試験体の表面または表面近くにある欠陥の位置や形状を検出する方法です。
磁気探傷試験はオーステナイト系ステンレス鋼などの非磁性体材料には適用できないことは覚えておきましょう。
放射線探傷試験(RT)
試験体に放射線を照射して投下後の放射線の強さの差を写真フィルム上に濃淡の像で現し、欠陥の有無や形状を検査する方法です。
放射線透過試験は材料中の内部欠陥、特に溶接部や鋳物における検査に広く使用されています。
超音波探傷試験(UT)
試験体に超音波を照射し、試験体中の欠陥による超音波の反射や散乱から欠陥の有無や形状を検査する方法です。
波長の短い超音波を使用することで指向性が強くなり、かつ欠陥による反射率が大きくなるため欠陥の位置検出精度を高めることができます。
渦電流探傷試験(ET)
交流電流を流したコイルにより時間的に変化する磁場を試験体に加えたとき、試験体に生じる渦電流が試験体中の欠陥、形状、寸法、電気伝導率などによって変化することを利用して欠陥の有無や形状を検査する方法です。
渦電流探傷試験は線、棒などの製品表面の傷や熱交換器チューブの割れや腐食の検出などに使用されています。
アコースティック・エミッション(AE)試験
材料が外力を受けて変形、または破壊するときにエネルギーが解放され、その一部が弾性波、主に超音波として放出されます。
この音波の放出をアコースティック・エミッション(AE)と呼び、発生したAEを検知することで材料の変化を知る試験方法です。
AE試験は材料に外力が加えられている状態、あるいは材料中に応力が生じている状態でなければ実施することができません。
まとめ
高圧ガス甲種機械の検定試験範囲である、保安管理技術についてまとめました。
過去問を中心に内容をまとめましたが、問われやすい分野というのは確かにあるようです。
そこを中心に勉強しつつ、細かい内容までどこまで詰めるかですね。
ひっかけ問題が意外に多いので、本番では問題文を落ち着いてよく読みましょう。ゆっくり解いても時間は余るはずです。